Construction contractors rely on accurate estimating to win bids and stay profitable; streamlining their estimating process can save both time and errors while improving business standing within its industry. With help from construction estimating service, advanced software, and best practice can significantly boost estimating efficiency.
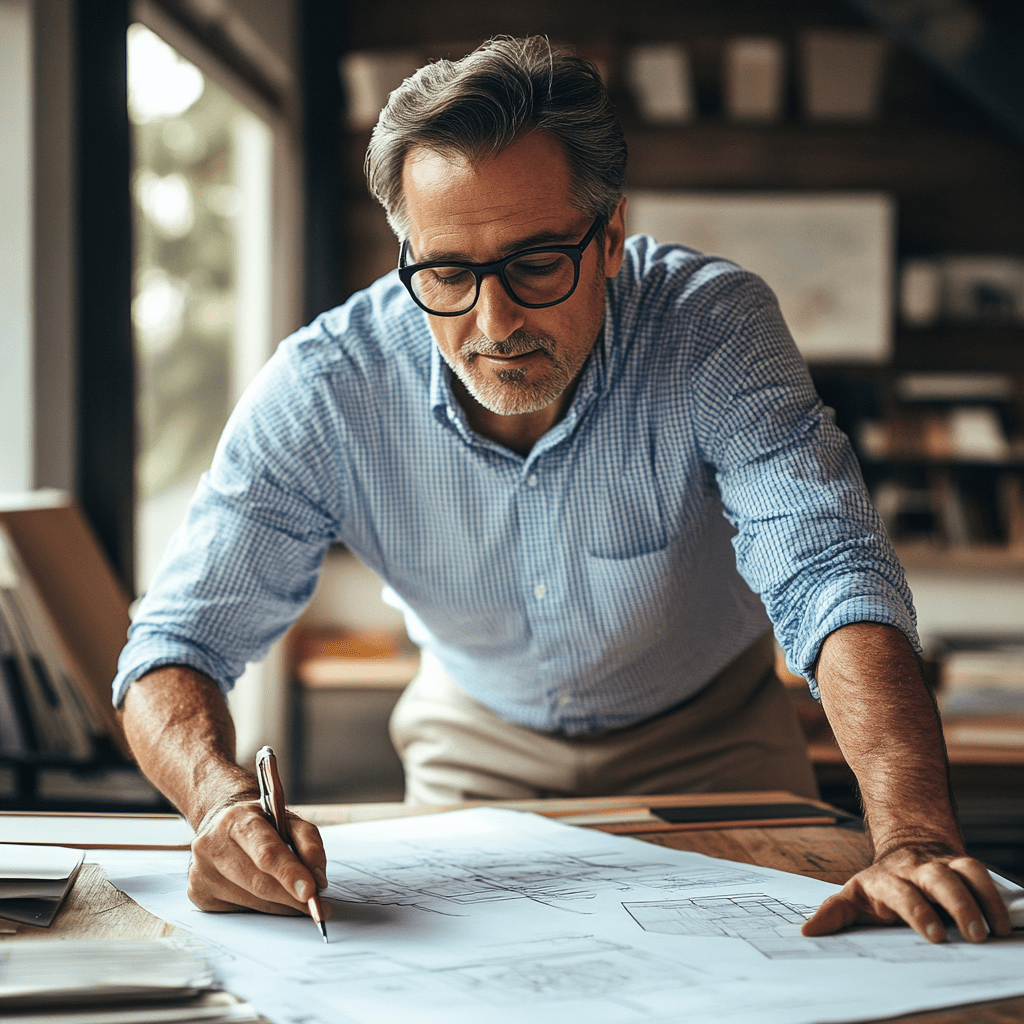
This guide offers key strategies and tactics for producing accurate, timely estimates, from cost breakdowns to structural steel detailing estimates. At the conclusion of this article, you’ll possess all of the knowledge and tools to optimize your estimating process.
Accurate Estimates Are Essential in Construction
An estimate serves more than just cost calculations; it provides the basis for project planning, budgeting and execution. Accurate estimates are essential.
Winning More Bids: Competent and accurate bid estimates increase your odds of successfully landing more projects.
Avoid Overruns: Underestimating costs could result in financial losses while overestimating them could put off potential clients.
Enhance Profit Margins: Precise estimates help ensure projects fall within their specified profit margins.
Maintain Client Trust: Being upfront with estimates will build credibility and long-term relationships with clients.
Steps for Generating Quick and Accurate Estimates
1. Leverage Technology and Software Solutions
Manual estimation can be both time consuming and subject to human errors, making the manual estimation process inefficient and inaccurate. Modern construction estimating services now offer digital solutions which simplify this process for them by using modern software estimating systems which offer digital solutions which streamline this process and include tools which offer:
Automated Calculations: Automated calculations can reduce estimation errors for materials and labor cost estimation.
Cloud Access: To facilitate real-time collaboration among team members.
Prebuilt Templates: Save time with prebuilt estimation formats that offer more standardized estimation procedures.
Integrate With BIM/CAD: Increase precision through using 3D models and detailing insights when conducting structural steel detailing projects.
2. Outline Costs Accurately
An extensive cost breakdown gives greater transparency, helping avoid discrepancies between anticipated expenditure and actual expenditure. Some key components include:
Material Costs: These expenses pertain to raw materials like concrete, steel, wood and insulation – including their prices and pricing structures.
Labor Costs: Wages for workers, subcontractors and specialists.
Equipment & Tools: When considering this category of investments, take the cost associated with renting or buying machinery and tools into consideration.
Overhead/Indirect Costs: Permit fees, insurance premiums and administrative expenses should all be factored into overhead/indirect costs.
Profit Margins: These percentages must cover unexpected costs in order to remain profitable, including unanticipated expenditure and should account for unexpected expenditure.
Employ Historical Data & Industry Benchmarks to Gain Competitive Edge
Analyzing past projects helps contractors more accurately estimate costs. Analyzing historical information provides invaluable insight into:
Monitoring Material Price Fluctuations: Staying abreast of market trends is imperative in order to avoid cost miscalculation.
Labor Productivity Rates: Being aware of how long tasks typically require can help improve productivity rates and efficiency.
Comparing Similar Projects: Comparing costs against similar projects can reduce uncertainty.
4. Evaluate Structural Steel Detailing Services
Steel detailing services provide contractors with accurate cost estimates of steel projects and fabrication plans including;
Material Specifications: Type, grade and quantity requirements when purchasing steel products are key considerations when buying them.
Connection Details: For applications involving welding, bolting and fastening.
Erection Sequences: Step-by-step assembly plans ensure smooth implementation.
Calculations of Load: Ensuring compliance with safety standards and regulations.
Precision steel estimates ensure accuracy while mitigating unexpected expenses. By including detailed steel estimates in projects’ cost estimations and managing them more precisely, accurate steel estimates ensure maximum precision while mitigating unexpected expenditures.
5. Partner With Estimating Companies
Many contractors turn to professional estimating firms for help when conducting estimates in order to save both time and ensure accuracy. These firms specialize in:
Estimating Details Accurately: Employing advanced tools and databases for precise calculations.
Cost Comparison and Optimization: Comparing various material and labor options and optimizing them accordingly.
Time Saving Solutions: Focusing the energies and efforts of contractors solely on execution will reduce manual workload and save both time and energy.
Risk Analysis: Proactively considering potential cost escalation scenarios and mitigating financial risks is vital in successfully managing costs, mitigating future cost escalations risks and maintaining long-term success in managing expenses.
6. Deliver Regular Updates On Estimates
Construction costs vary significantly depending on several variables, including:
Material Price Changes: As supply chain challenges and inflation drive materials costs up and down significantly, material costs often fluctuate greatly from month-to-month.
Variations in Labor Market Conditions: Access and wage rates have an undeniably profound influence on total labor costs.
Changes to building codes and compliance regulations: New building code requirements can incur extra expenses.
7. Verify Measures and Quantities with Accuracy
Measurement errors can have devastating repercussions. Therefore it is imperative that measurements are carried out accurately so as not to incur such expenses and allow unforeseen omissions or errors;
Apply Digital Takeoff Tools: Measuring materials and quantities precisely is made simple using these digital takeoff tools, making measuring more straightforward.
Verifying Plans & Drawings: Verify that architectural and engineering designs are accurate.
Be Sure to Cross Check With Suppliers: Before finalizing estimates, double-check material specifications and costs with potential suppliers.
8. Consider Potential Costs In Case of Emergencies
Every estimate must include an emergency contingency budget to plan for unexpected circumstances, typically 5–10% of total project cost should be set aside as insurance against unexpected costs such as:
Design Amendments: After starting their project, clients often request changes that modify design elements.
Weather Delays: Severe weather can often delay work schedules.
Supply Chain Disruptions: Delays in material delivery.
Conclusion
Estimators who handle estimation themselves or hire professional estimators should prioritize consistency and continuous improvement as top priorities in their estimation services.
Learn More : Foundation Repair Cost in 2025: Affordable Solutions for Homeowners
FAQs
1. What are the functions and responsibilities of construction estimating firms?
Construction estimating firms provide professional cost estimation services to contractors. Their experts assist contractors with accurate project budgeting, material takeoffs and risk evaluation – giving their bidders an advantage in bidding.
2. How will structural steel detailing impact construction estimates?
Structural steel detailing helps ensure accurate fabrication and assembly plans, decreasing material usage while simultaneously increasing timelines, timeliness accuracy and compliance to engineering specs.
3. What tools are effective for construction estimation?
Popular tools include PlanSwift, Bluebeam Revu, STACK and ProEst; each offers digital takeoff capabilities with cloud storage options to facilitate efficient estimating processes.
4. How can contractors increase estimate accuracy?
Contractors can increase accuracy by employing estimation software or consulting construction estimating companies; reviewing historical data; performing material takeoffs with meticulous detail and accounting for contingencies.
5. How should my construction budget accommodate contingencies?
As part of any financial preparations for any project, 5-10% of its costs should typically be put aside as an emergency reserve in case unanticipated expenses come up and to maintain financial security throughout the journey.